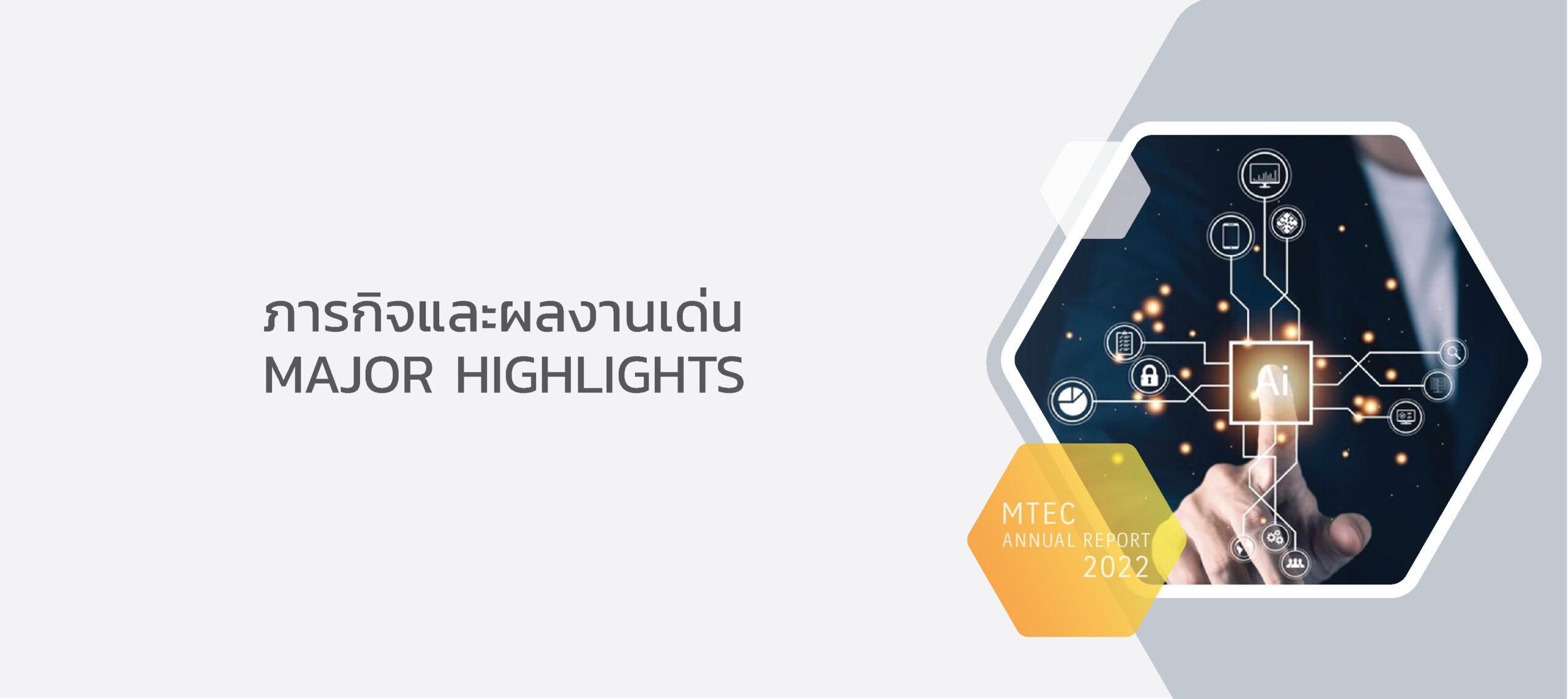
Name
Skill Preparation and Know How Development in Designing and Manufacturing of Pick-Up Stay Side Steps from Plastic Composites
Background
An increase in competition in the automotive industry makes Thai auto part manufacturers to regulary modify the part designs and their production processes. In order to increase the competitiveness of automotive part making, it is necessary for the part manufacturer to develop knowledge in designing and producing parts by themselves.
The most popular material used in the manufacture of automotive load-bearing parts is steel. Many efforts have been used to develop various features continuously to make the steel thinner or lighter while maintaining comparable strength properties to the original. This aspect always contributes to the energy savings.
However, with the existence of alternative materials e.g. engineering or advanced plastics, many automotive parts could be made even more lighter and at lower cost than steel. To make automotive parts from plastics, modification in the part design and material selection based on considerations in the functions, strength, service temperature range and working conditions of the part must be considered.
In addition to this, manufacturing process needs to be consistent with the part design. Generally, forming of plastic parts comprises fewer steps than steel forming for example injection molding of plastic is a one step process with which the manufacturing cost is greatly reduced compared to manufacturing of steel parts.
Modern tools such as computer-aided engineering and process simulation are increasingly playing a role in nowadays material replacement works. In summary, knowledge of the design, material and manufacturing process are required factors in developing of a metal replacement plastic part having satisfied overall quality and cost.
Goal
- Skill preparation and know how development in designing and manufacturing of plastic parts & molds and injection molding
- Development of stay side step prototype from plastic composite having acceptable mechanical properties and weight reduction between 10-20% compared to the original material.
What does the research team do?
First perform the material selection experimental to acquire the suitable type of plastic material for the stay side step, then design the part using CAD and CAE to analyze the strength. Then conduct the injection molding simulation to design a suitable injection mold. After the injection mold is built, produce stay side step workpieces which underwent the pre-listed test criteria. Stay side steps workpieces are both passed all the test standards and has reduced weight as desired.
Research results
Prototype of stay side step made of plastic composites with mechanical properties that meet the specified standards and 23.75% weight reduction compared to the original part.
Research status
completed
Research team
Dr.Patcharee Larpsuriyakul, Dr.Wuttipong Rungseesantivanon, Dr.Bunpot Mai-ngam, Dr.Sutee Olarnrithinun, Natcha Prakymoramas, Jareenuch Rojsatean, Dumrong Thanomjitr, Sanya Kaewket, Pasayapurin Promprapai, Papan Panyavan and Atapol Palasay
Contact
Dr.Patcharee Larpsuriyakul (Senior Researcher)
Plastic Product Development Research Team
Material Processing and Manufacturing Automation Research Group
Tel. +66 2564 6500 ext. 4449
Email: patcharl@mtec.or.th